Aluminum refining impellers
EuroGraphite offers its own range of graphite impellers that can be used for various degassing purposes. Our specialists will help to simulate the flow regime, melt circulation, gas saturation process and select the appropriate design of the impeller.
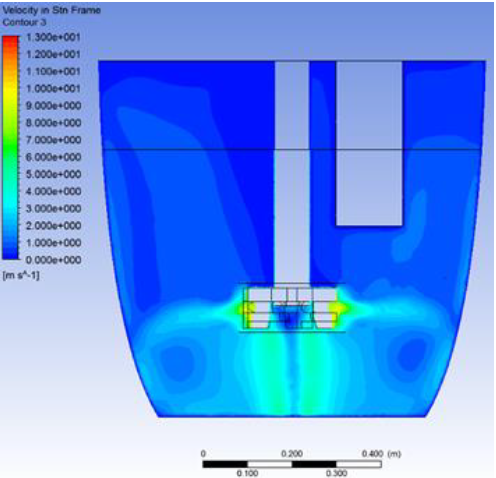
Simulation of vertical circulation
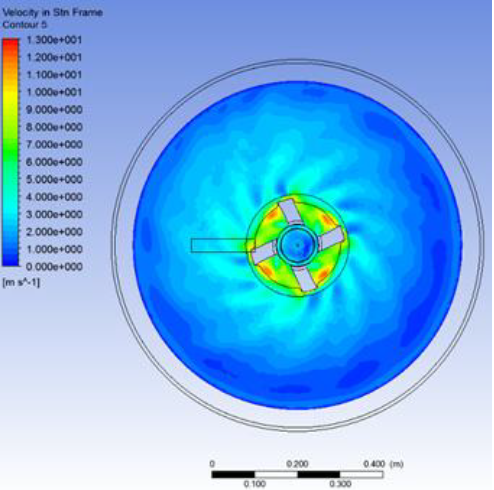
Simulation of radial flow
impellers F2 и F2A
The task that was set during the development of the F2 and F2A impellers was to saturate the melt with a cloud of finely dispersed gas bubbles over the entire volume of the tank. In particular, so that the circulation of the metal and its contact with the gas cloud created by the impeller is carried out even at the bottom of the ladle.
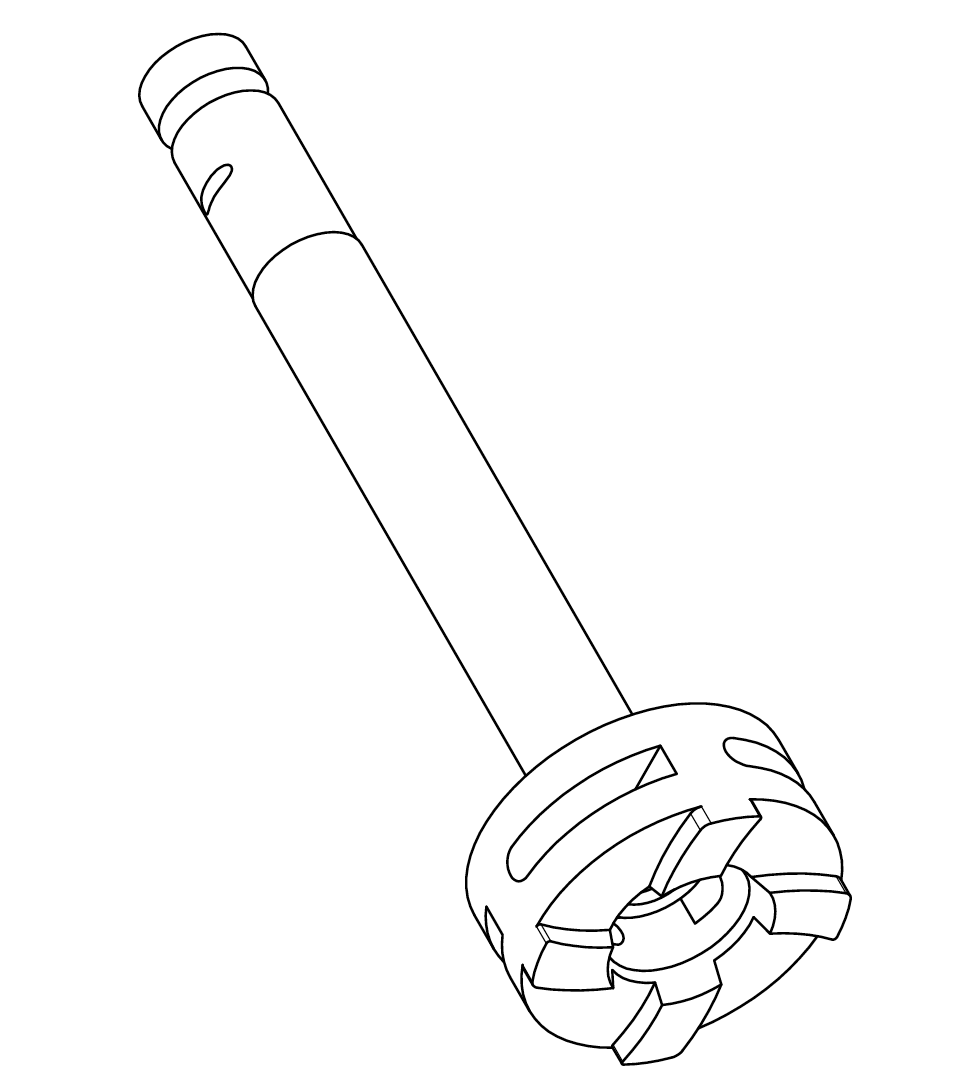
Impeller F2
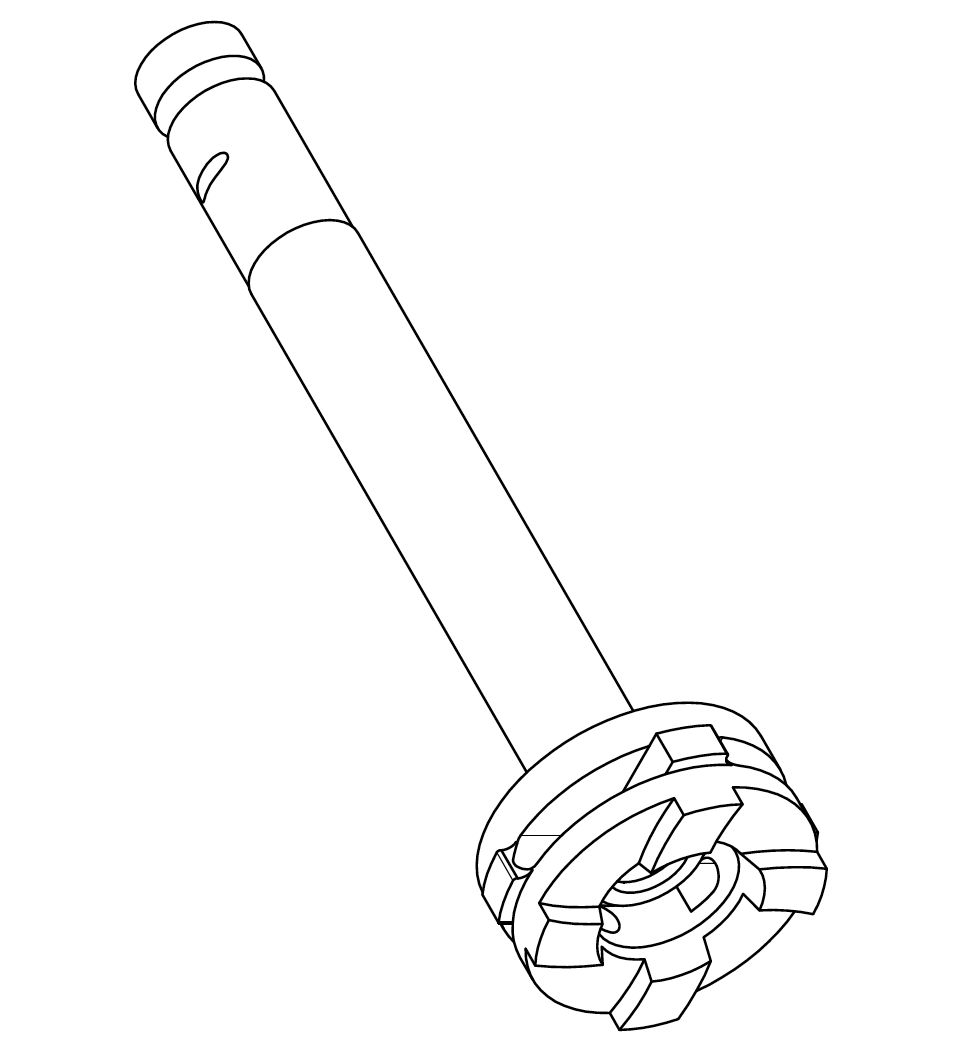
Impeller F2A
The design of these degasifiers creates an effect similar to centrifugal pumps. The rotor draws the molten metal from the bottom of the ladle and mixes it with the gas supplied through the hollow shaft. Then, under the influence of the centrifugal force created by the rotation of the rotor, a mixture of molten metal with inert gas is ejected from the impeller. The impellers also have the effect of producing a cloud of fine bubbles emerging from the radial channels of the rotor. A cloud of gas bubbles dissolves in the molten metal and binds hydrogen and other impurities inside. To increase turbulence, small side vanes were added to the outer surface of the rotor.
The most important features of the F2 and F2A impellers are:
1. Curved radial vanes at the bottom of the impeller. These blades direct the radial flow down and create a strong vertical circulation in the ladle, lifting the metal from the bottom of the ladle. For maximum effect, we recommend choosing the shaft length so that the impeller is approximately 200-300 mm above the bottom of the bucket.
2. The F2A impeller, in addition to good mixing of metal with an inert gas, creates very strong turbulences. Sufficient to pull fluxes off the surface.
3. Also in the line of rotors there is a modification F2B, which is applicable together with a conical shaft in those cases when, after the first stage of degassing, it is necessary to pull off the fluxes at a high rotation speed, after which, at the second stage, to keep the surface of the melt in a laminar state.
impeller G1
The G1 impeller is well suited for applications where it is not possible to mount the rotor very close to the bottom of the bucket. It also works equally effectively under conditions of changing the direction of rotation, creating strong turbulence and mixing of the melt with gas in all directions.
Even with very long use, the partial destruction of the rotor blades retains its ability to create intense mixing.
At the same time, it should be noted that this type of impeller creates very strong flows on the surface of the melt and may create a risk of contamination of the metal with impurities drawn from the slag layer.
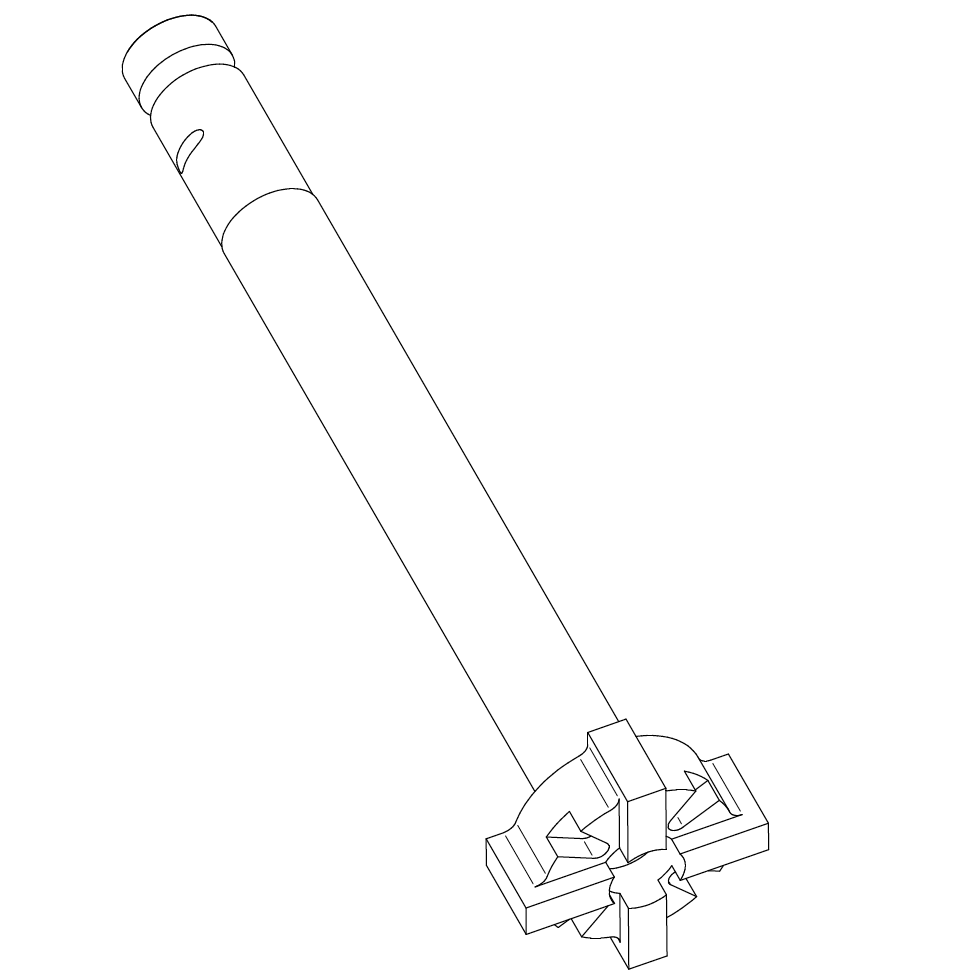
impeller G1
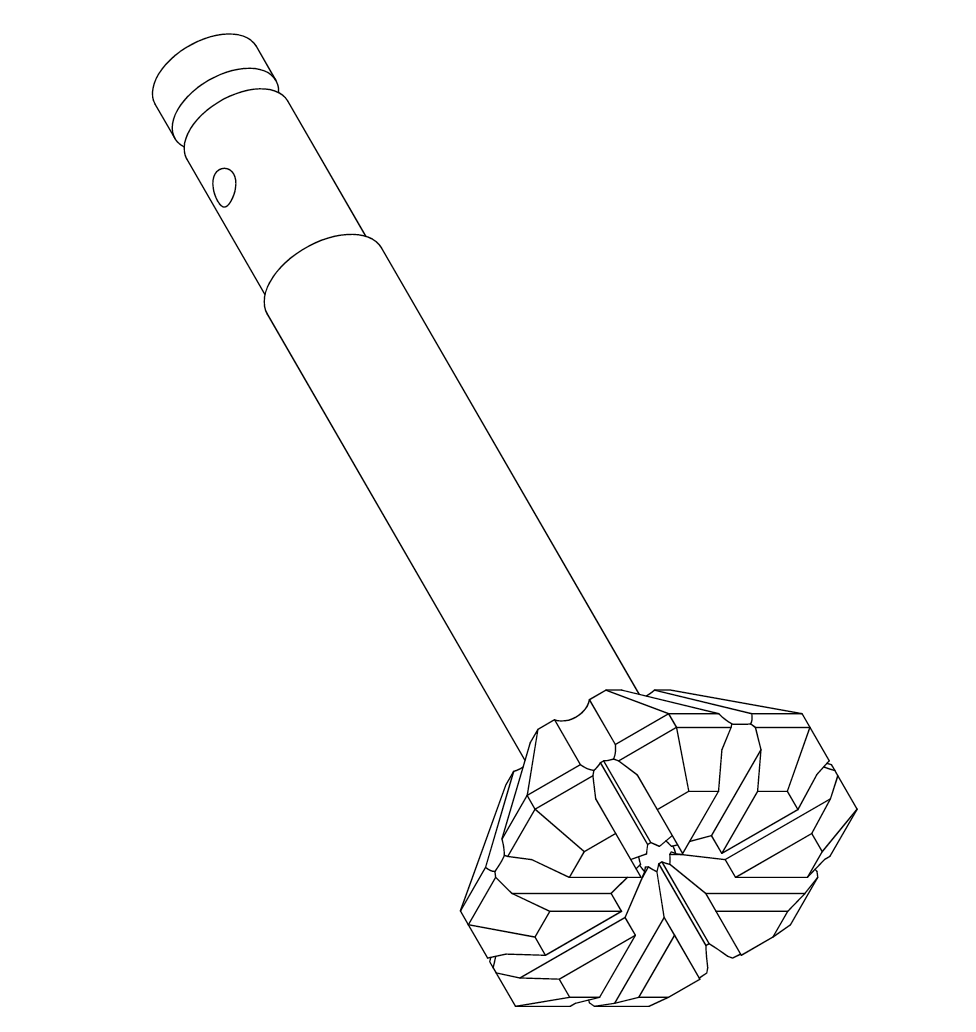
impeller J8
impeller J8
The development of the J8 impeller was initiated by foundries that do not use fluxes in the process and degassing does not require strong flows and eddies on the surface.
On the contrary, this process involves the saturation of the melt with a stream of small bubbles of inert gas in a calm state, without intensive mixing.
The best use of the J8 rotor is when the distance between the rotor and the bottom of the bucket is 100-150mm.
J8 impeller is very durable compared to other models, and its surface is relatively streamlined, which has a positive effect on the service life. Experience in industrial operation has shown that even partially worn rotors effectively perform their function.
All types of shafts and rotors are impregnated with a special antioxidant developed by our company to maximize the life of graphite parts. The final stage of impregnation is heat treatment, which stabilizes and crystallizes the antioxidant. Crystallization increases its volume and part of the antioxidant falls on the surface of the parts in the form of a white precipitate.
The impeller is wound onto the lower end of the shaft. To protect parts from damage during transportation, the shafts and rotors are packed in cardboard boxes.
We recommend our customers to allow the rotor to run over the ladle for a few seconds after it has been lifted from the molten metal (if safety conditions permit).
The rotors listed above are patented by the European Patent Office.
Contacts
GDI Technology s.r.o.
- Czech Republic, Brno, Tkalcovska, 874/3a, 60200
- +420775543330
- ed@gditechnology.cz
- Telegram: +79831549944, WatsApp: +420775543330